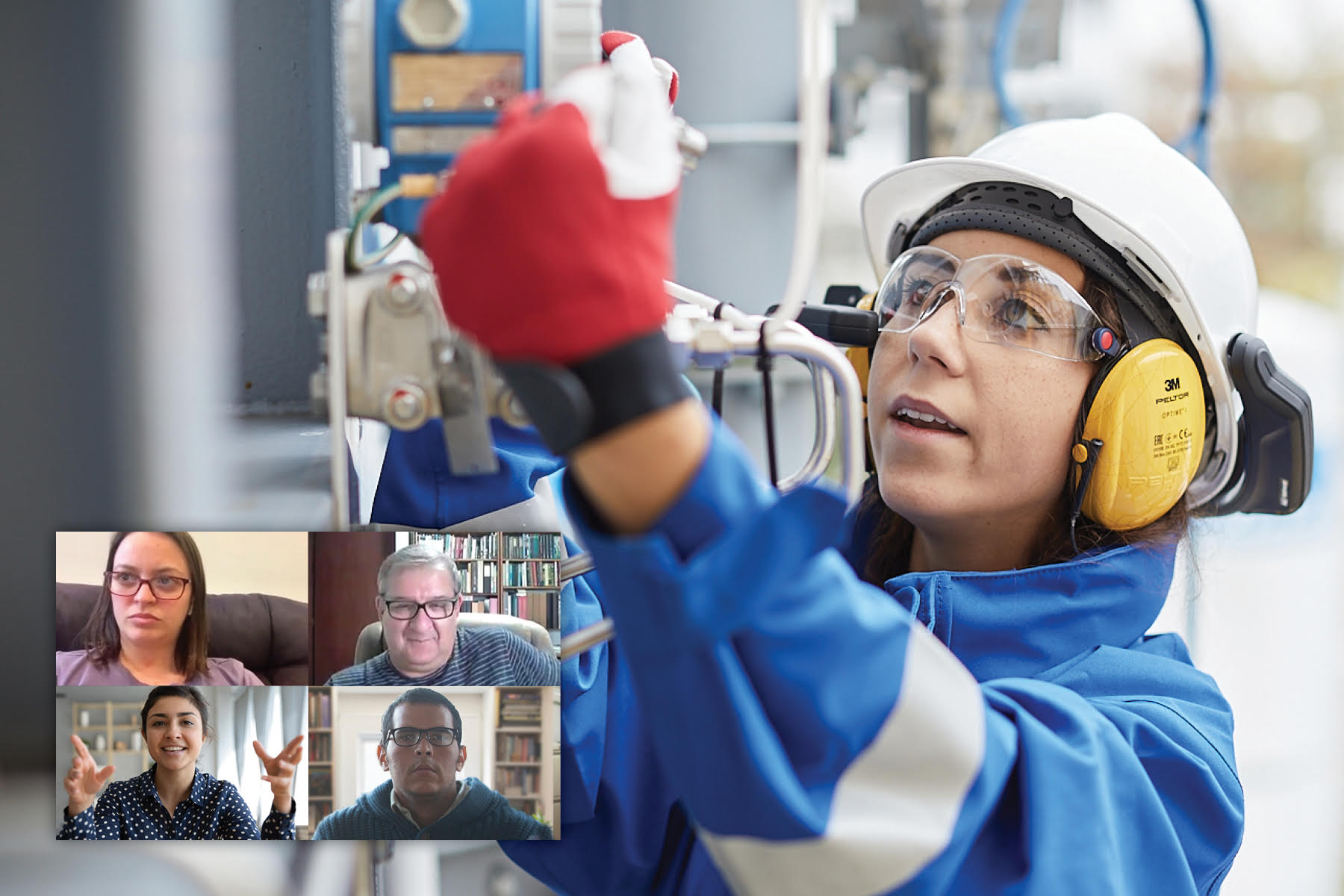
Automated industrial technologies are some of the most powerful tools at the hands of modern business owners, and they are constantly changing and getting better. While industrial automation has mostly been used in manufacturing, more small businesses are using automated industrial technologies to increase productivity and efficiency in their offices as well as on their factory floors, warehouses, and supply chains. Using industrial technology can mean more efficient manufacturing, more timely deliveries, faster response times to customer inquiries, less wasted materials and supplies, fewer accidents on the job site, lower turnover rates – all things that add up to increased profits for your business in the long run.
With access to large amounts of data from sources such as IoT technology and existing machinery, organizations can observe trends and make informed decisions about how best to improve efficiency. Artificial intelligence is also an emerging technology that can help companies become more productive by optimizing workflows at every level of production. For example, AI can help prevent human error in complex systems or find better ways to set up equipment for enhanced output.
Over time, businesses have had to continue to invest in technology to keep up with economic changes and maintain productivity. With technological advances, there is a significant increase in production speed, quality of product, quality of life for employees, and efficiency of output.
Advanced technologies can save time and money by doing tasks faster and more accurately than a human would be able to do them by hand. Advanced automated industrial technologies have allowed industries to be more productive which has led to increases in overall efficiency for production. Additionally, these new technologies allow humans who work alongside automated systems to spend their time on more creative or important projects rather than tedious ones.
Technology is coming into its own when it comes to industrial automation. The internet of things, or IoT, refers to interconnectivity between objects and devices that were never designed to talk to each other. When applied effectively in a manufacturing setting, these connected devices can predict problems before they happen. They can speed up processes by using predictive maintenance and even set machinery at optimal levels based on real-time production data. These applications are game-changers in industrial automation—but they won’t be fully realized until we see significant growth in IoT use cases. By then, most smart products will connect wirelessly with one another without needing an on/off switch or charging station.
Many industries are now choosing automated industrial technologies to improve their work productivity. Currently, the steel and food processing industries are early adopters in this space and are using industrial automation, but it has become more popular in all sorts of different industries and sectors as the benefits have proven to be well worth the costs of upgrading.
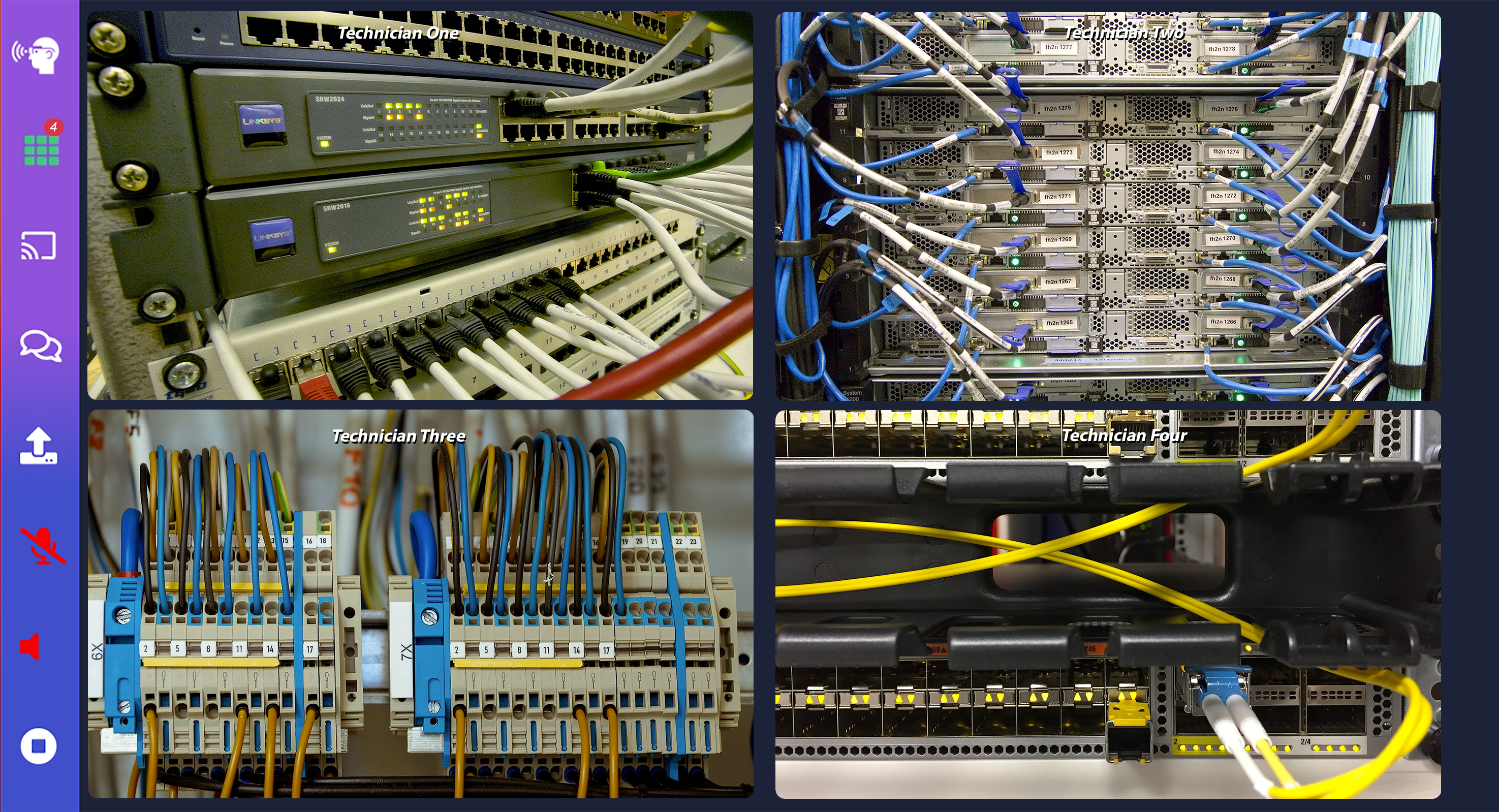
With many companies already investing in industrial automation software to streamline processes and boost productivity, those who haven’t gotten on board are in danger of falling behind. As technology advances, factories must keep up with new tools and techniques that allow them to turn out goods faster, better, and cheaper than ever before. While newer versions of industry-specific software are introduced regularly, one thing remains constant: businesses depend upon it to stay competitive and productive.
Small productivity boosts compounded over time can save a company millions of dollars. Automating a complex task like QA testing can save hundreds of man-hours. Automatic testing can catch issues more systematically and quickly to avoid costly shutdowns.
As more industrial automation technologies become commercially available, more companies are deploying them in factory settings. In turn, more workers can operate machinery with fewer errors and less fatigue. These machines also have improved efficiency, which means fewer resources need to be used in production. Automation is here to stay. As technology continues
Workers also benefit from industrial technology. Automatic safety sensors can help workers avoid dangers they can’t see, smell, or hear. Wearable devices help keep technicians’ hands free to hold railing or keep their balance in compromising conditions.
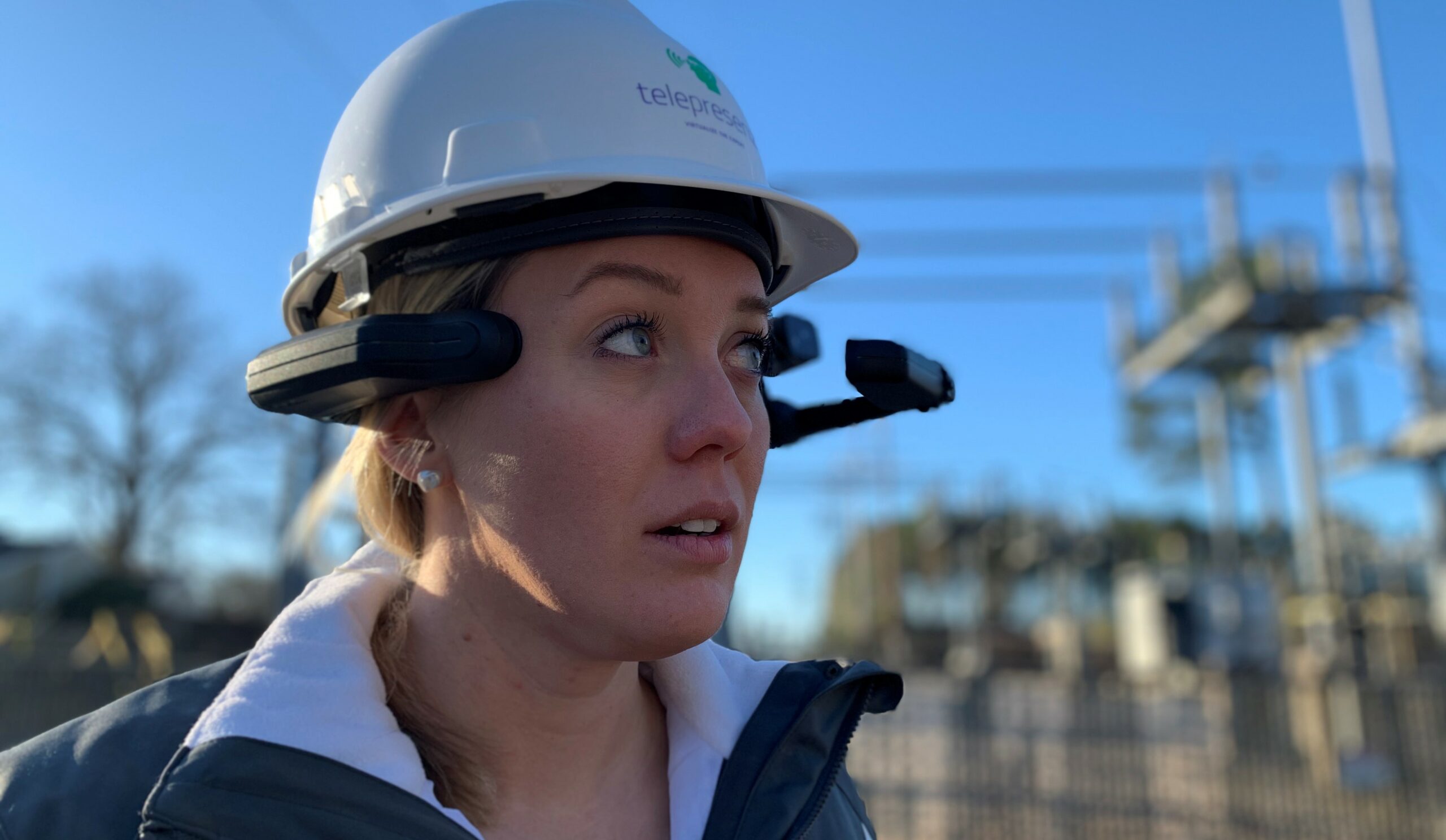
In today’s increasingly mobile and distributed workforce, employees need access to office productivity tools no matter where they are. Tools like document sharing, chat, and video conferencing bring people together in new ways, but cloud security is often an obstacle to increased collaboration. Telepresenz’s remote collaboration and workflow management software integrates with industrial automation software options, offering manufacturers a way to enable remote workers to access information and optimize data use no matter where they are.
As technology advances, manufacturers are finding more and more uses for industrial automation. By automating manual labor, companies can produce products faster and cheaper than ever before. Automation continues to become more intelligent as engineers work to make robots that can think for themselves. With these advancements in artificial intelligence, there’s no telling what our world will look like in 5 years – or even 20! Whatever happens, it’s clear that automated industrial technologies are going to play a big role.